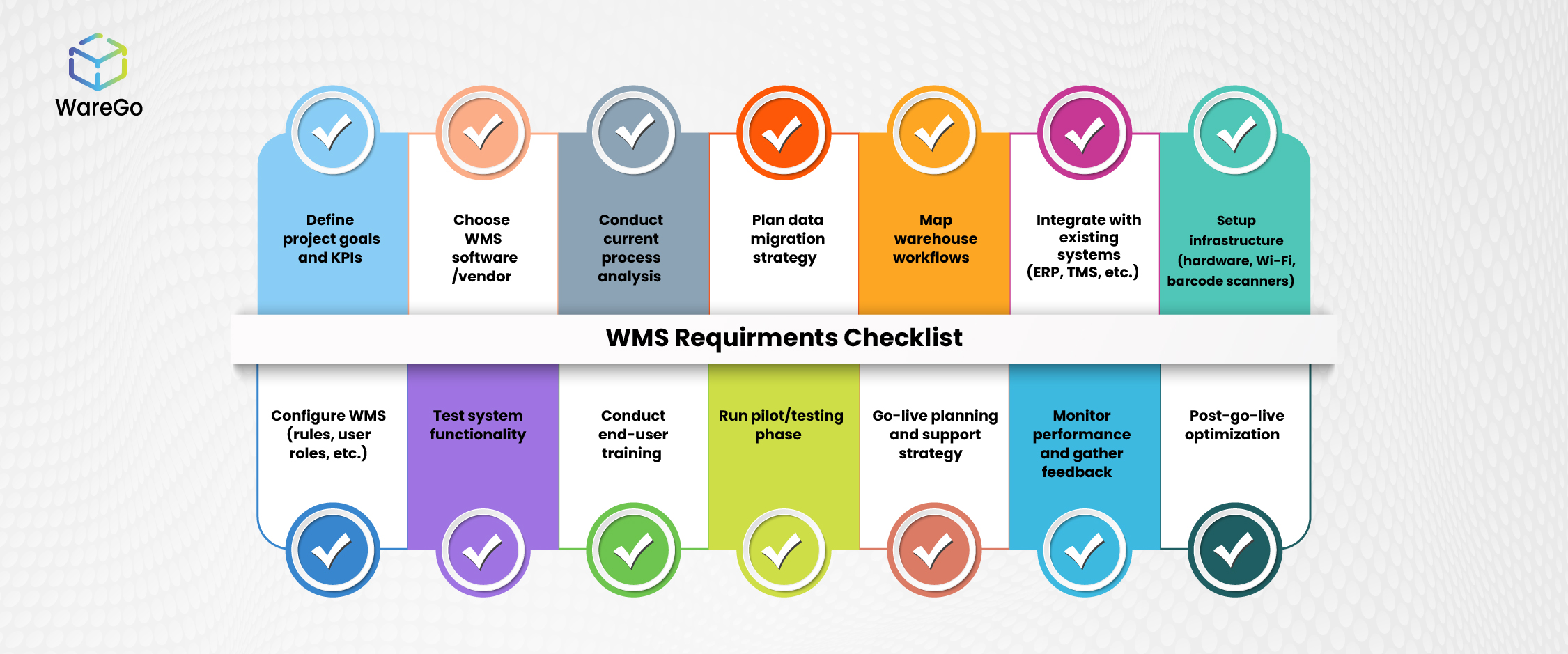
Are you planning a Warehouse Management System (WMS) implementation in 2025? If yes, we understand that you are likely searching for a clear path to successful WMS implementation. While generic WMS implementation checklists provide basic details, they are not helpful for the practical elements, like steps, costs, etc.
Keeping that in mind, we have written a different blog post. Our blog post provides a clear, easy-to-understand blueprint that educates readers with more than the basics. We have included all necessary WMS implementation steps, an actionable checklist to keep at hand, and other important considerations like implementation costs.
If you are a warehouse or distribution center manager/owner and have been noticing a disorganized warehouse, inventory count is mostly inaccurate, and delivery times are often slow, this article is a starting point for optimizing your warehouse for better productivity and efficiency.
Table of Contents
Your 2025 WMS Implementation Checklist [All Checks for Successful Implementation]
Before we move to in-depth, lengthy steps of how to set up a warehouse management system, let’s give you a quick WMS implementation checklist to keep at hand. Our strategically proven checklist starts below.
Note: We have divided our checklist into 3 major phases for your convenience.
Pre-Implementation
- Adopt the SMART goal-setting method to begin with. This means that objectives for WMS implementation should be set in a smart, measurable, achievable, relevant, and time-bound manner.
- Identify all the key stakeholders in your warehouse and make sure they are well-engaged throughout the implementation process.
- Make a document that includes every process of your current 3PL WMS software and the pain points present in terms of the warehouse operations.
- Develop a vision board for where you see your warehouse in the future. This includes increasing inventory levels, complexity of operations, and more.
- Make a dedicated team that looks after the WMS implementation process and assign clear roles and responsibilities to avoid confusion.
- Build a foolproof strategy for data migration (refer to our steps section for more details on this) and list requirements, if any.
- Search the market, look for reviews, and shortlist the top vendors for WMS software.
- Make a comprehensive RFP (request for proposal) to learn more about the vendor and their offerings.
- Opt for demos and consider online or offline meetings to ensure your needs and the vendor’s vision are aligned.
- Consider a pilot program or POC (proof of concept) with the chosen vendor.
- Finalize the selection process of the vendor and contract negotiations. Here, an important point to be noted is to ensure that to pay attention to SLAs so that you do not come across any surprises in the future.
Implementation
- Create a comprehensive WMS implementation plan that is detailed with timelines and milestones.
- Carry out the configuration process of your new WMS as per your requirements and warehouse needs.
- If your vendor offers a customization option, make sure you customize it with clear documentation to achieve the necessary outcomes.
- Migrate the data from the old WMS to the new WMS and make sure to validate it for accuracy.
- Make detailed testing plans and execute them to check that everything is working in its ideal way.
- Make sure a clear communication path exists between the WMS implementation team and the stakeholders from all departments.
- Conduct training sessions for the team to make them familiar with the WMS. Also, develop end-user training materials.
- Work on the strategy of going live. Decide whether you want to roll out at once or need a phased plan.
- Make a rollback plan just to be on the safe side (in case some error occurs).
Post-Implementation
- Roll out the go-live plan.
- Provide Hypercare to the users so that they don’t feel alone with the new WMS.
- Keep a close check on the performance of the WMS system and note if any issues or shortcomings arise.
- Look out for feedback from the users and address any concerns presented by them.
- Go for post-implementation reviews and see if there is a space for improvement or optimization.
- Make sure that ongoing training and support are provided to the team managing or using the WMS.
- Instead of implementing the WMS and leaving it, carry out a WMS data analysis to understand trends and possible opportunities.
- Invest in regular scheduling of system updates and maintenance to ensure your WMS is up to date at all times.
- Check the ROI based on the objectives set in the initial stages.
WareGo brings ease of implementation to its clients by managing the entire implementation process, ensuring you get an efficient WMS with 0 hassles.
Sign Up NowHow to Set Up a Warehouse Management System? [WMS Implementation Steps + Proven Tips]
While a checklist helps you learn all it takes to successfully implement a WMS, a detailed process is vital to understand how each step works and how to make the process successful. This section includes 4 WMS implementation steps with tips and advice to ensure you get the most out of your WMS investment.
Step 1: Strategic Alignment & Needs Assessment
Way before you consider WMS features and opt for vendor demos, it is vital to understand that the success of 2025 WMS implementation is a result of the strategic alignment of your needs and goals with the WMS. This means that before moving towards choosing a WMS software for your business, it is important to assess your needs. During this step, you must understand the reasons behind your decision to implement a WMS. These reasons include every fundamental driver and the outcomes you aim to achieve after implementing the WMS. Missing out on this phase is like sailing without a clear destination in mind. You might feel like you are moving towards success, but you will be unable to achieve the desired WMS benefits.
1. Defining Crystal-Clear Objectives
It is a commonly known fact that every warehouse or distribution center seeks improvement with a WMS software implementation. However, generic aspirations like “increased efficiency” or “enhanced inventory management” would not lead you to success. Thus, if you are willing to get the most out of a WMS software, you need to define goals that are not only crystal clear but also measurable. This means you need to move beyond the generic overviews and identify the specific KPIS (Key Performance Indicators) you expect in return by implementing the WMS.
The following table will explain more about the difference between generic and specific goals and objectives.
Generic Goals | Specific Goals |
Improved Order Accuracy | Ensure that order errors are reduced by 15% in the first 6 months after implementing the WMS. The number of orders shipped incorrectly will measure this. |
Decreased Cycle Times | Beginning from order placement to shipping, reduce the average time of the order fulfilment cycle by at least 24 hours during the first year. |
Lower Labor Costs | Gain a 10% reduction in the overall warehouse management labor costs per order with the help of optimized pickup routes and efficient task management within the first 10 months. |
Enhance Inventory Visibility | Get a 99% accuracy level across all stock-keeping units. This will be calculated by regular cycle counts and physical audits. |
When you set specific, measurable, achievable, relevant, and time-bound (SMART) goals, you make a standard against which the success of your ecommerce WMS implementation can be tested. This clear setting of goals helps you choose the right vendor for your needs and helps you learn about the implementation strategy and post-go-live optimization efforts.
2. Ensure Stakeholder Engagement
A WMS implementation seems like an IT project, but clearly, it is not. It is a transformation point of the entire warehouse and affects every part of its operations and beyond that. Therefore, during the implementation process, it is essential to involve all teams of every department of the warehouse. Consider taking on board the stakeholders of:
Department of Stakeholders | Why Are They Needed |
Operations | Operations teams are the daily users of the system, and no one understands workflow and pain points better than they do. |
IT | It is crucial to take the IT team on board as they are essential for technical integrations, infrastructure, and continuous support throughout the process. |
Finance | Finance people are important too, as they are the ones tracking the ROI and managing the overall budget. |
Customer Service | Once the WMS is implemented, it has a direct impact on order fulfilment and customer satisfaction, therefore, the customer service team is important to take on board. |
Sales & Marketing | Sales and marketing personnel are important for sales forecasts and other promotional activities. |
Involving these stakeholders is necessary and builds a sense of ownership, allowing them to share their unique perspectives and help identify roadblocks before they become hurdles for your warehouse operations. Other essential elements to consider include:
- Communicating the benefits and vision of the new WMS to be implemented to every stakeholder.
- Asking for their input to identify ongoing challenges, required improvements, and system needs.
- Decide on clear communication paths and regular meetings to make sure all stakeholders are fully aware of the ongoing process.
- Consider managing all elements that different teams come across, including timelines, disruptions, and the amount of involvement expected from each of them.
While some might think involving the stakeholders is not as necessary as stated, ignoring them can lead to things like a lack of buy-in, resistance to the new WMS, and overall less successful implementation of WMS. Apart from technicalities, it is worth considering that a collaborative approach helps in building a strong foundation for adopting a new system and welcoming long-term success.
3. Future Proofing the WMS Implementation
While most vendors would not inform you on this, there is more to think about than immediate needs. To make the implementation actually strategic, you need to consider how your warehouse would look in the coming 3 to 5 years. What will be the update in terms of demand in your target market, advancement in technology on your operations and plans regarding the efficiency and growth of your system
You can future-proof your WMS implementation with a quick exercise that involves brainstorming and documenting. This exercise must include the following questions:
- For growth projection, ask yourself how you expect your order volume to change. Will you be handling more SKUS or different types of products?
- In terms of technological advancements, ask yourself whether you will be planning to consider elements like automation, robotics, or advanced analytics in the near future. Will the WMS need to integrate with these technologies?
- Considering customer expectations, will delivery windows be tighter than this? Will there be increased demand for customized orders or services?
- In terms of supply chain evolution, how will changes in your supply chain impact your warehousing needs?
By considering the image of your future warehouse, you are likely to make a wise decision about choosing the cold storage WMS vendor and make the implementation successful.
Step 2: Vendor Selection & Due Diligence
Once you are fully aware of your needs and have a future vision in hand, the next step is to learn how to choose a warehouse management system vendor. And to catch you off guard, this step is not just about selecting a software package with a list of fancy features. It is more about creating a long-term relationship with a vendor who understands your business goals, has an idea of supporting businesses in growth, and aligns perfectly with your long-term business vision.
1. Understand the Pillars of a Successful Partnership
A retail warehouse management software functional capabilities are important, but considering only the features can become a shortsighted approach in the long run. For a successful implementation of WMS, you need to consider more elements like:
Partnership With the Vendor
While there are multiple vendors available in the market, try looking for the one that actually understands your industry and the business challenges companies face. Look whether they offer proactive solutions and insights for common problems warehouses come across? Do they have a history of client appreciation and positive relationship building? Picking a vendor with a collaborative approach is important, as such a partner will work for you and with you.
Check for Support & Training
To handle an efficient WMS, you need to have an efficient team. And for that, look for vendors’ training programs, availability of resources, and ongoing support services. Also, another thing to consider is the responsiveness of the vendor, the expertise with which their support team works, and the different channels with which they offer support.
Flexibility and Scalability of the WMS
While choosing a WMS, you need to keep in mind that your business will evolve over time and your WMS needs to adapt to it. To choose a WMS, check whether it has the scalability to handle future growth in terms of volume, SKUS, and complexity. Make sure you consider the flexibility, as it comes in handy for accommodating the changes in processes and integrations with other systems.
Industry Expertise of the Vendor
Finding a vendor who already has experience in the industry you work in is nothing but a blessing. Having such a vendor means they are better aware of the unique challenges your business faces, have better practices to make warehousing easy, and have improved regulatory requirements. Their experience and insights can help streamline the entire implementation process while ensuring your system is configured enough to meet your needs.
For a better understanding, you can look for references from similar companies to yours. Make sure the references are based not only on the software’s functionality but also on the overall experience.
2. Utilize the Vendor Compatibility Scorecard
If you cannot assess the credibility of a WMS vendor on your own, you can consider using a vendor compatibility scorecard. This tool goes a step further than the technical specifications and helps in evaluating other important aspects of potential vendors. The criteria of this compatibility scorecard include:
Cultural Fit
This point checks whether the values and communication style of the vendor align with yours or not? If cultural fit is strong, it can offer a smooth collaboration and an improved, positive long-term relationship.
Alignment of Long-Term Vision
Does the vendor have future plans and a roadmap that meet your long-term strategic goals? Is the vendor focusing on areas that are important for your business in the coming years?
Checking the Communication and Responsiveness Level
This scorecard helps in evaluating the responsiveness of vendor in the initial process. It helps in evaluating whether the vendor is trustworthy enough to offer reliable future support. Also, to identify how transparent and clear the communication of their support team is.
Proactiveness and Innovation of the Vendor
It checks whether the vendor has a proactive approach towards the client and provides innovative and helpful solutions. It also helps in understanding whether or not the client is investing time and budget in research and development.
Stability In Terms of Finance
The scorecard helps ensure that the vendor is stable in financial terms and is a reliable partner in warehousing needs in the long term.
To make the decision, assign specific weights to every element of the criteria as per your priorities, and then score the vendor in accordance with them. This approach is not only structured but also offers a comprehensive and objective assessment that comes in handy in identifying a vendor whose values and vision are well aligned with your warehouse or distribution centre needs.
3. Do not underestimate the Importance of Pilot Programs (POCs)
Initially, discussing features looks like all you need to do while choosing a WMS that works for your business. But as discussed, it is not the case. Consider taking a live test in your warehouse environment to ensure WMS and the WMS vendor align with your expectations. The concept of pilot programs and POC (proof-of-concept) comes in handy to make a sound WMS decision in such situations.
A strategically made POC includes:
- Check the warehouse management system’s capabilities in a real-world scenario with your data and workflows.
- Evaluate whether the WMS can be integrated into your warehouse’s existing systems, like ERP, TMS, etc.
- Understand the friendliness of the WMS system and ask your team for feedback.
- Look out for the vendor’s implementation methodology, support, and responsiveness.
- List potential challenges that you see during the testing, and refine your needs before going for full-fledged implementation.
Going for a POC is a brilliant way to identify whether your needs and the WMS in consideration align. Another great tip is to treat this step as a learning opportunity and a way to eliminate the chances of costly surprises.
Step 3: The Ultimate Implementation Roadmap
Once the step of selecting the WMS vendor successfully ends, the crucial step of implementation begins. But if you are planning to have an implementation plan that is rigid and does not have a space to adjust or change, you are likely to come across problems, especially in today’s ever-evolving business landscape. Instead, going with a flexible approach can get the job done while having leverage to change as the needs change.
1. Agile vs. Waterfall – Pick the Methodology that Best Fits Your Needs
If you are willing to go with the typical traditional “Waterfall” methodology, it follows a linear approach that goes in sequence. This approach includes requirements gathering, design, implementation, testing, deployment, and maintenance. In comparison to this approach, there is the “Agile” methodology that works a bit differently than the traditional method and uses an iterative development, breaking down the project into smaller cycles (sprints) with frequent feedback and adjustments. When a WMS implementation is considered, both of these methodologies have pros and cons, and learning each of them is essential to make the right decision.
Waterfall
Pros | Cons |
A properly defined scope from the beginning | Do not have the flexibility to adapt to the ongoing changes. |
Clear documentation on each step of implementation | Issues might come into consideration in the later stages of implementation. |
It is easier to manage for less complex implementations with stable requirements. | Does not perform efficiently for the ever-changing needs of businesses. |
Agile
Pros | Cons |
Has the ability to adapt to changing business needs. | Requires a team with strong WMS insight for continuous collaboration and feedback. |
Developing and sharing parts of the software more often, instead of waiting until everything is finished | Since the scope can evolve, an efficient team needs to be onboard for active participation and learning. |
Provides space for ongoing feedback and collaboration. | |
Let’s help you identify issues and mitigation problems during the early stages of WMS implementation. |
In general, going with a waterfall methodology does not work due to its complex nature and the fact that challenges may arise during the process. Therefore, agile or hybrid methodologies work best in such scenarios where implementation is divided into smaller stages that are easy to manage and focus on specific modules and functionalities. This way, you can achieve success in quick way, collect user feedback in the early stages, and adjust the implementation as per the real-world experiences presented to the warehouse.
2. Strategy to Migrate Data
For a warehouse, old or new data is the most important element, and operations largely depend on it. Therefore, migrating the old data to the new WMS is a crucial step and must be taken before the WMS is implemented.
For successful data migration, make sure you include the following points in your strategy:
- Data cleansing and validation are essential steps before the data is migrated. Invest time to do so. Look out for inconsistencies, errors, and redundancies in your data and correct them. Remember, having useless data with you will only generate useless results.
- Map how your present data fields will collaborate with the data fields in the new WMS. This is done by data mapping and is important for compatibility.
- Go for phased migration to make the process convenient. This way, you will be able to migrate the most important data first and the less important data later.
- For accuracy and consistency, test the data right after it is migrated to the new WMS. Here, a conciliation process will also help in comparing the data in the old and new WMS.
- Instead of migrating the data and deleting it, keep a proper backup for rollback in case any issues arise during the migration process.
3. Consider Micro-Implementations Instead of Going Live at Once
Most distribution centers and warehouses believe in going live at once, where they roll out the entire WMS in one go. But this approach has some pitfalls. We suggest that you consider the micro implementation strategy. In this strategy, you divide the implementation process into smaller and manageable phases.
Wondering about what benefits you get with micro implementation? Check out below:
- Reduced Risks
- Faster Time-to-Value
- Improved User Adoption
- Iterative Learning and Adjustment
- Better Resource Allocation
See the following examples of micro implementations phases to get a better understanding:
With the help of a clear and strategic roadmap that includes agile methodology, a certain data migration strategy, and a micro implementation approach, you can ensure WMS implementation that works perfectly for your warehouse or distribution center.
Step 4: Going-Live & Post-Implementation Optimization
Once the WMS software goes live, you feel like all the work is done, and now you can sit back and enjoy the ultimate efficiency it brings to your warehouse operations. Well, to burst your bubble, this is not the case. Going live with your WMS is the beginning step of new things like user adoption, stabilization, and continuous improvement. The process after going live can be divided into the following steps:
1. Comprehensive Training Programs for Better Outcomes
While initially, the features and functionality of a WMS are the most important thing, having a team not trained properly to use the WMS can make things worse for your warehouse. Therefore, well-planned training programs are essential to keep the team well aware of how the system works, updates, and other changes. Keeping the following in sight will also benefit:
Training As Per the Roles and Responsibilities
To make the training process convenient, divide the training sessions according to the roles and responsibilities among the employees. For example, the training of a picker is not the same as the training of the supervisor, so make groups and then offer training.
Offer Hands-on Learning Instead of Theory
The theoretical talking does not gel in with the team as a practical hands-on training would; therefore, practical training should be opted for in an actual working environment. Let the users understand the system and become familiar with its functionalities.
Make Sure All Resources are Easily Accessible
Instead of making the WMS learning a guessing game, go for making training materials easily available for the teams. These materials can be anything from user manuals to video tutorials, FAQs, and more. The goal is to offer users as much information as possible so that they can get help with any difficulty they might come across during the initial getting to know the WMS.
Make a Training Team Instead of Training Everyone at Once
Training the entire team at one time might seem like doing a hard job in an easy way, but it is not always the case. This approach has a lot of potential to spread confusion, making the team understand literally nothing. That’s why they should pick a few members from each team and train them to train everyone else on their team. This divide and rule method will surely make it a success.
Training the Refresher for Better Results
Instead of once-in-a-while training, go for regular refresher training sessions to make sure employees are up to date with effective practices and new features and address any issues the team may be going through.
The User Adoption Strategies
While functionalities and mechanics must be communicated to the team, the benefits and other efficiencies a WMS adds to the warehouse are also important to be delivered. To every employee, try communicating the ease a WMS adds to their role and make them feel benefited by the entire implementation. Also, you can ask the users for their feedback and how they think procedures can be improved.
Opting for detailed and regular training makes your employees confident about the WMS, which ultimately increases the software’s potential and helps with the users’ convenience in adoption.
2. Manage The Critical “Hypercare” Period With Care
The time right after the WMS implementation is crucial and in most cases, critical and sensitive. During this period, the user (your warehouse employees) is getting familiar with the new workflows and overall changes in the way tasks were executed before. To cope with this, a hypercare period can be implemented to make sure everything is stable and users are confident.
The hyper care method must include the following elements:
- A dedicated team to help the users whenever an issue arises.
- Quick response time so that users do not have to wait till the problem resolves.
- Physical support should be there so that the team has someone to reach out to in times of emergency.
- A system should be made where issues are listed and resolved in a timely manner.
- Daily meetings should be held with the representatives and stakeholders to stay ahead of the issues the team is facing with the WMS.
- A predefined procedure for the escalation of issues must be there to keep everything disciplined, even in terms of need.
Hypercare might seem like an extra step, but it will prove to be vital once you execute it, as it helps in catching the problems and issues in the initial period of WMS implementation rather than leaving them ignored till they become bigger concerns.
Don’t get confused by hundreds of WMS vendors claiming to deliver the best solutions. Opt for a free trial to make the decision.
View Packages5 Common WMS Implementation Challenges & How to Overcome Them
While we have discussed how to implement the WMS software, it is worthwhile to learn about the common challenges that might occur and how you can overcome them.
1. No Clear Objectives
One of the challenges that often results in failed implementations is having no clear objectives of what you are looking for. When you do not have a clear understanding of what you need, you end up choosing the wrong WMS software. There are hundreds of WMS software vendors, but would you pick the one that works best for you?
Solution:
Instead of going for WMS demos and shuffling through the proposals, take some time to evaluate what you are searching for. Make a document where you list down the efficiencies you want to add to your warehouse operations, what gaps you need the WMS to fill, and what features are must-haves for you, keeping the next 3 to 5 years of your warehouse operations in mind. This way, you make sure to pick the right WMS vendor with the help of clear objectives.
2. Inadequate WMS Testing
Most warehouse managers choose software by looking at its features and warehouse management system cost, or just by word of mouth. While it looks like a good approach, having improper testing or no testing at all can get you in a lot of trouble. This not only affects your warehouse operations but also wastes a good sum of money.
Solution:
Look out for WMS vendors who offer pre-testing or a trial period, as it will help you make the right decision. During testing sessions, identify all issues that occur, like delays in integration, improper functioning of WMS, or other performance issues. With WMS testing, you need to be sure that it is working properly to avoid any issues in the future.
3. Overlooking Your WIFI Speed
Most WMS, like WareGo, operate online and are known as cloud-based WMS. If you are opting for such a WMS, overlooking the need for a robust internet can get you off guard.
Solution:
Make sure you take a reliable internet connection provider on board and a technical team to ensure internet connectivity is up and running at all times. Remember, implementing a brilliant WMS in your warehouse with a poor internet connection will do no good to operational efficiency and cost you a fortune instead.
4. Poor User Training
As discussed earlier in the article, user training is a must if you want to enjoy all WMS benefits. Most of the time, the training part is overlooked, thinking it is an online software and will be used as per the written instructions that come with a WMS. If you, too, think the same way, we suggest you think again before this challenge becomes a hurdle.
Solution:
Train all stakeholders of your warehouse and other relevant teams thoroughly right before you implement the WMS. If training the entire team seems a hurdle, consider training two to three people from each team so that they can guide and train the team easily. You know, the divide and conquer rule never fails.
5. Not Considering Future Warehousing Needs
A warehouse or a distribution center is always likely to expand its operations. However, if you neglect this fact and pick a WMS based on your current data needs, you will likely face challenges in the near future. Some WMS software does not come with a customizable or scalable nature, and this often becomes a hurdle when warehouse management needs expand.
Solution:
To combat this challenge, you can make a vision board of how your WMS might look in the near future in terms of warehouse management needs, data, team growth, and more. Once you get future needs clear, you are all set to choose a WMS software solution for your warehouse.
WMS Implementation Costs Made Smarter with WareGo
WMS implementation costs vary according to the vendor under consideration. There is no one price tag to mention since hundreds of different vendors are working in the market, and each charges different fees depending on the nature of WMS, the features it has, the implementation complexity, and more.
But we, at WareGo, have some brilliant news for you. If you are willing to invest in a SaaS WMS software to automate your warehouse operations, our WMS is all you need. To help make the implementation process convenient for our users, we charge no implementation charges to ensure customers stay within budget while implementing their warehouse management system.
Our WMS packages have 3 variants to make your selection convenient. Explore all 3 to pick the one that aligns best with your warehousing needs.
Unlike most WMS providers, we prioritize our clients getting their WMS implemented at no cost. Choose high high-quality experience with WareGo today.
Contact UsConclusion
Manual warehousing is no longer the right way to deal with modern logistics needs and ever-increasing customer demands. Therefore, WMS software is in the market to help warehouses and distribution centers automate tasks and improve their operations by reducing errors and elevating efficiency. While the process sounds intimidating, having a clear WMS implementation checklist at hand can make everything a lot easier. So, no matter if you are switching from your old WMS to the new one or implementing the WMS for the first time, our guide has everything you need.
Frequently Asked Questions – WMS Implementation
What is WMS implementation?
WMS implementation is a process of setting up and deploying a WMS (warehouse management system) to automate tasks, increase efficiency, optimize the operation, and manage the entire warehouse. During implementation, you need to integrate WMS with the existing software, like ERPs or more, configure the functionalities, train the warehouse management software team, test, and ensure WMS performs smoothly.
What are the Four Types of WMS?
The four types of best warehouse management systems (WMS) include Standalone WMS, Supply Chain Execution Modules (SCM), Integrated ERP Systems, and Cloud-Based WMS. Each of these WMS has its own benefits and serves different needs of warehouses and distribution centers. To implement the right WMS for your business, evaluate your needs and pick the one that matches them perfectly.
What is the WMS Implementation Process?
The WMS implementation process includes several phases: teams begin with initial planning and vendor selection, then train staff, test the WMS in a real environment, and finally go live. The implementation process is complex and requires careful coordination and vigilant attention to details in order to get the most out of the WMS benefits.
How to set up a warehouse management system?
There are several steps to take into consideration when setting up a warehouse management system. These steps include defining goals, choosing the correct WMS vendor, doing the necessary preparation for the warehouse, and finally implementing the system with proper testing and training of staff. However, here, it is important to understand that businesses need to know their needs and the functions of WMS to set it up correctly.